Anomaly detection systems are essential in various industry applications. With computer vision (CV), they can search for and pinpoint visual elements deviating from the norm. It helps optimize workflow and enable the efficient execution of tasks. There are many variables to consider when designing or using vision anomaly systems, especially when used for a custom solution.
Computer vision based anomaly detection systems used in industry usually consist of hardware and software components. The structure of the technical components allows bottlenecks to emerge at the software, hardware, or integration level. On the other hand, the operational factors surrounding each industry's applications introduce tradeoffs and challenges that vary across and within different industries. Engineering professionals, quality control experts, and domain experts continually work together to squeeze every last drop of accuracy, performance, and resilience from computer vision-based anomaly systems.
This article examines the quality and operational implications of employing different forms of computer vision-based anomaly detection systems in the manufacturing industry.
Anomaly Detection in Manufacturing Using Computer Vision
Defect detection tasks in manufacturing commonly include predictive maintenance, quality control, process optimization, safety monitoring, root cause analysis, inventory management, demand forecasting, or logistics. As part of the Industry 4.0 initiative, computer vision-based anomaly detection systems introduce advanced methods to handle such tasks and improve manufacturing processes.
In manufacturing, computer vision systems analyze images and videos captured at various stages in production lines or processes for unusual patterns, events, or deviations that may indicate potential problems or defects. Computer vision systems for identifying anomalies in manufacturing lines can take several forms, ranging from product defects and process deviations to safety hazard identification. By adopting computer vision, manufacturers can enhance product quality, optimize productivity, increase efficiency, minimize safety hazards, improve precision, and reduce downtime.
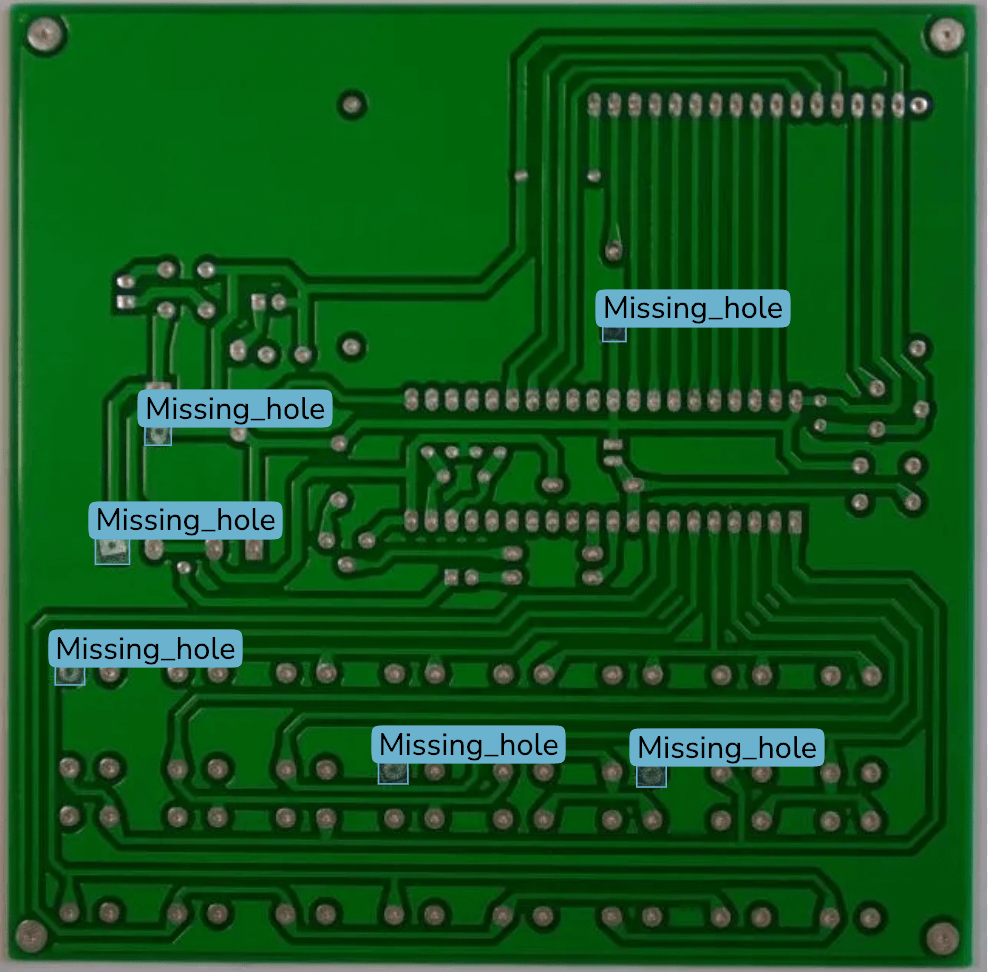
Anomaly Detection with Computer Vision Systems in the Manufacturing Industry
The systems may consist of stand-alone machines with integrated software and hardware, like a robot, or exclusively of software that manufacturers can integrate with any hardware, such as cameras and frame grabbers.
These systems' modes of operation and design dictate their flexibility, scalability, and efficiency at the development, operational, and team levels. As such, each systems solution, from its technical to its operational approach, has a significant effect on the team and product in terms of cost, operation, scalability, e.t.c
Computer vision-based anomaly detection systems are more economical than traditional inspection methods. However, there are cost of non-quality (CONQ) concerns to pay attention to when employing them. In a nutshell, these systems are products with a process from development to manufacturing line deployment. The choice of design determines the value of the system.
No Feedback Systems
No feedback systems typically provide a plug-and-play solution. They are specifically developed to manage limited visual defects or processes in manufacturing lines. They tend to thrive in banal circumstances when visual anomalies are rare in certain stages of the production process. They are beneficial when used in settings with minimal improvements needed due to data drift and assistance to humans in the loop. After being deployed in manufacturing lines, there is no need for extensive training or data collection.
There is no inclusion of the manufacturer's engineering teams in the active development of this type of system. Therefore, manufacturers may need help tracking solution performance in the manufacturing line. Only the solution's vendor can fully maintain and fix these systems. It can be ideal for manufacturing companies that are interested in something other than investing in engineering and operations teams.
Given that it is a black box with no traceability, the cost of non-quality for these systems can be very costly and difficult to measure. It can take a lot of time to figure out when it begins to fail. Failure can result in high rates of false positives or negative defect detection. More costly repercussions arise if defective manufactured products reach end users. The development process to adjust this system could be more agile, which could further lead to downtime in operations. Solutions like these are inexpensive in the long term due to their limited data requirements and development costs, as long as they don't fail. Stemmer imaging provides this type of solution.
Partial Feedback Systems
These systems may offer a platform or interface that enables observability and analytics to monitor and measure production lines' efficiency. In-house operations, product, and quality teams can use the feedback from the system to create processes in the manufacturing lines and further optimize workflows. They can quickly gain insight into the degradation or data drift of the defect detection system. They can then deduce the possible causes from environmental and operational factors that occur over time. This information is shared with the vendor responsible for developing their vision systems to speed up development iteratively. The detection of defects is continuously data-driven, increasing the chances of delivering quality products from the manufacturing lines. This system also reduces the workload and cost of running operations and product teams, as there is no in-house development team.
The vendor and manufacturing teams are involved in a partial feedback workflow. Data collected during production is used to fine-tune the vendor's computer vision anomaly detection algorithm. Manufacturers, however, are not involved in the development process and must be made aware of how the vendors provide the solution based on the data. This gap leaves the potential for privacy and security concerns, especially for delicate data involving intellectual property or personally identifiable information (PII). Manufacturers risk losing data if they quit the solutions, which can stunt their growth. They also need to be made aware of the type of computer vision anomaly detection model the system uses.
Although it eliminates the hassle of development and makes operations seamless, it limits the ability of the manufacturers to scale further or optimize their internal workflows across their teams and the solution. The implication is that manufacturers will need little to no developer teams. Therefore, there will be no need to acquire specialized experts. Even if the manufacturing team needs a development team, it doesn't need a team of highly skilled developers like machine learning, data, platforms, and DevOps engineers. This kind of vendor lock-in creates friction that can stifle innovation and prevent seamless workflow optimization. The long-term cost of this sort of system is high because manufacturers must constantly pay for the services the vendor provides. Some applications of this system are Deltia, Scortex, Cerrion, Ahx.ai, etc.
Full Feedback Systems
These types of systems allow manufacturers to develop their custom end-to-end systems. It enables a fully managed system that allows rapid development and operation processes. The system is flexible enough to support most standard hardware and software used in the manufacturing line. Internal teams can integrate their existing hardware and software stacks into these systems. It also provides the option of using straight-out-of-the-box tools and services. These tools and services are also customizable to fit the manufacturing line workflows.
It is a good option when trying to create a fully flexible, scalable, and optimized defect detection system for the workflows in manufacturing lines. The system could be improved to better handle the changes over time. Bottlenecks regarding the manufacturing line data and computer vision anomaly detection model are fully transparent, traceable, and observable. It also provides the luxury of selecting and swapping out anomaly detection models for various manufacturing use cases if manufacturing line requirements change.
In the long run, the cost and benefits of this system outweigh the initial investment in building a team and resources especially as it opens the capability to address an infinite number of use cases such as in logistics and employee safety. Picsellia is an end-to-end computer vision platform. It allows manufacturing companies to seamlessly migrate and integrate workflows and data from existing systems.
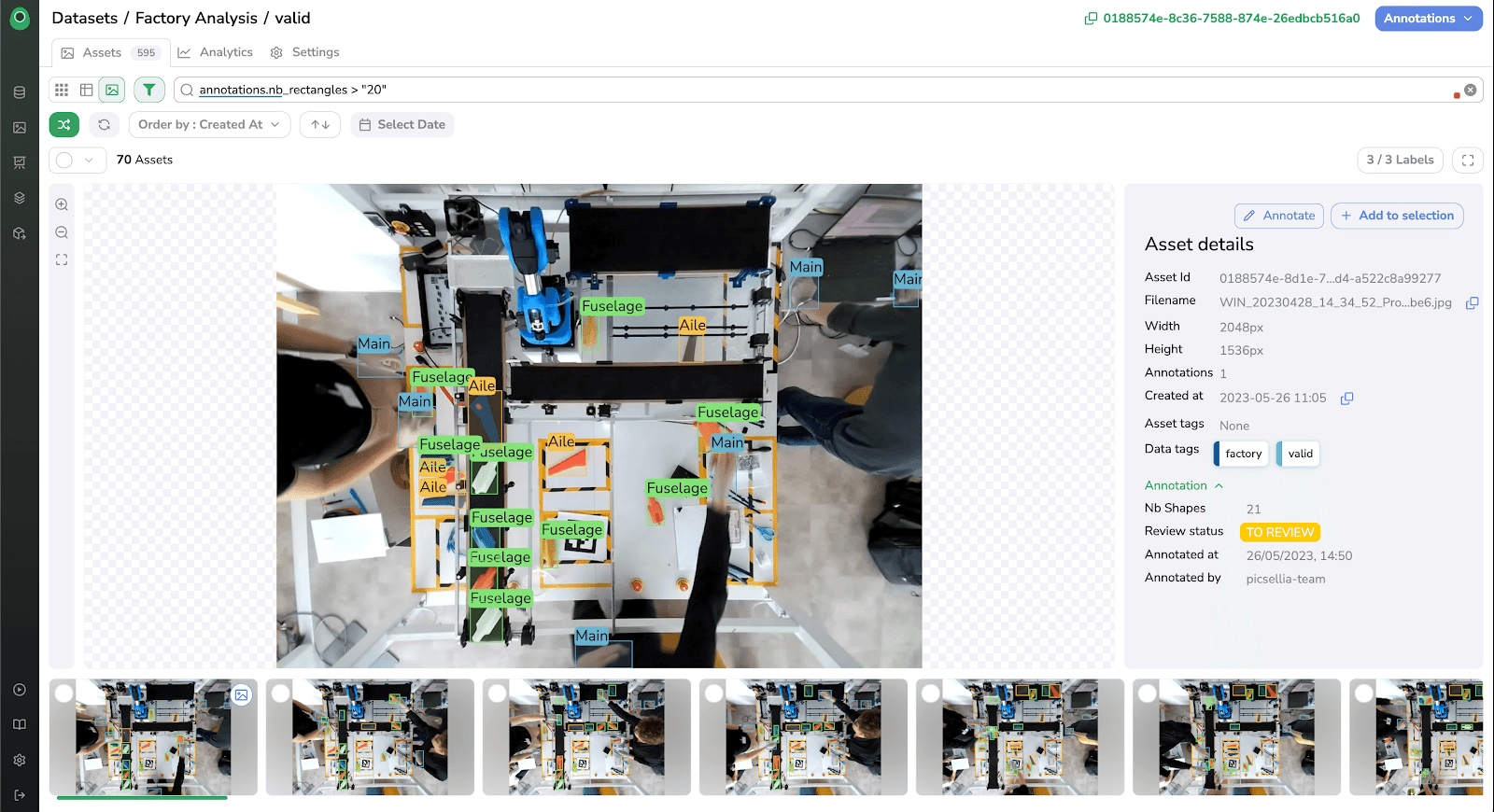
Benefits and Challenges of Anomaly Detection with Computer Vision Systems in the Manufacturing Industry
Computer vision solutions for anomaly detection result in peculiarities that enhance or limit teams and manufacturing processes from an operational standpoint.
Benefits of Anomaly Detection in the Manufacturing Industry
- Improving product quality to avoid product recalls and rework
- Optimizing production flow and saving downtime
- Identifying security breaches, unsafe work habits, and faulty equipment and improving safety
- Monitoring and analyzing industrial processes in real-time, continuously evaluating product quality, process efficiency, and safety
Challenges of Anomaly Detection in the Manufacturing Industry
- Implement a solid infrastructure that efficiently manages and enforces governance on data from the manufacturing process.
- Training, deploying, and maintaining computer vision models for robust systems are resource-intensive and require sophisticated techniques.
- Balancing the defect detection specificity and sensitivity results from the system.
- Being able to explain and interpret the results from these systems.
- Integrating computer vision systems with the manufacturing line's pre-existing control, automation, and data management systems.
Conclusion
Manufacturers can reap the benefits of improved product quality, optimized manufacturing processes, and greater safety by carefully addressing challenges and employing the latest advancements in computer vision technology. They also help optimize the workflows and operations of professionals in downstream or parallel teams. However, job displacement, data privacy, etc., are still some major ethical and societal concerns around its adoption.