Production lines (i.e., assembly or manufacturing plants) are the backbone of manufacturing industries. Tasks and operations on production lines requiring visual assessment are challenging to manage with human supervision.
Fortunately, modern manufacturing sectors quickly embrace smart technologies such as computer vision to eliminate inefficiencies in executing visual tasks. According to a report by Global Market Insights, Inc., the use of computer vision in the manufacturing sector alone is expected to surpass USD 6 billion by 2032.
How are manufacturing industries leveraging computer vision solutions to manage vision-based tasks and operations in their production lines?
This article highlights how computer vision addresses critical challenges and streamlines operations in production lines. Then, it showcases real-world examples of how industries successfully implement computer vision solutions and provides insights into what it takes to develop and deploy them for manufacturing.
Solving production line challenges with Computer Vision
Production lines are organized systems of robots or machines engineered to optimize efficiency, reduce errors, and maintain consistent product quality. Computer vision software enhances these systems, equipping them with the ability to perform complex visual tasks and operations more effectively, such as:
Part misalignment
Frequent movement and vibrations during the operation of machines and robots in production lines can cause parts to deviate from their proper calibration. These misalignments can lead to assembly or production errors, resulting in defects, rework, slower production, and increased costs.
Computer vision systems can detect and identify misaligned parts in real-time by analyzing images of products or machine components along the production line. When a misalignment is detected, the system can automatically trigger adjustments or send alerts for re-alignment, ensuring the process continues smoothly.
Defects detection
Product quantity inspections are critical processes typically performed between or at the end of production lines to ensure that only flawless products leave the facility. These inspections are often time-consuming and tedious for human supervisors. Additionally, some products may appear perfect but have minor defects that are difficult to detect manually.
Computer vision solutions automate the inspection and detection of product flaws that human inspectors might overlook, such as cracks, scratches, or improper assembly, drastically reducing the likelihood of defective products reaching customers.
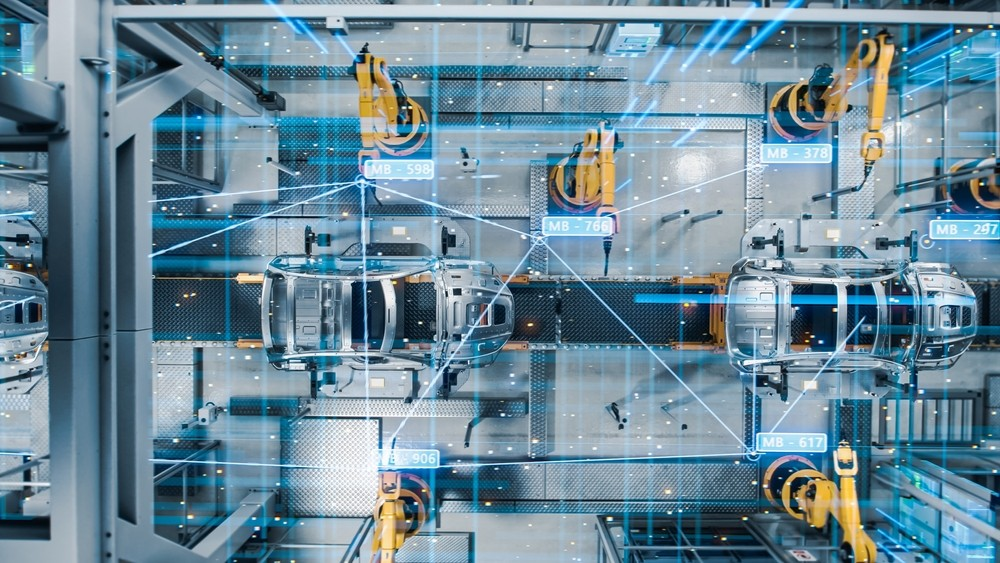
Traceability and compliance
Some manufacturing industries must strictly adhere to regulatory standards to minimize errors and enhance safety. They are often required to document production line procedures for auditing and compliance checks. Capturing reports that require visual documentation can be challenging due to the complexities of visual inspections, the subjectivity of visual assessments, and the sheer volume of data.
Computer vision solutions automate the capture of image and video data at various stages of production, seamlessly tracking and documenting every process. These systems reduce the chances of subjective assessments and ensure full traceability, helping industries maintain compliance with regulations.
Addressing these challenges with computer vision solutions improves efficiency and productivity, mitigates product errors, and ensures safety on production lines.
Applications of Computer Vision in Industry Production Lines
Industries rely on both specialized and standard machines in their production lines. The assembly of these machines varies according to the product being manufactured, the infrastructure layout, and the specific processes involved. Consequently, the vision-based tasks and operations on a production line also differ. Below are practical examples of how computer vision is applied across various industry production lines:
Automotive Industry: Quality control and defect detection
Case study: Using computer vision for surface inspection
An automobile manufacturing company must ensure that the surface quality of car bodies meets the highest standards, free from defects such as dents, scratches, or paint imperfections that could impact the vehicle's appearance and customer satisfaction.
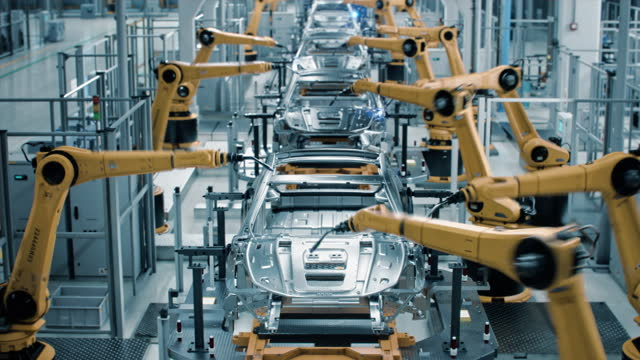
They developed a computer vision system that uses high-resolution cameras on the production line to inspect car bodies during manufacturing automatically. The system scans the entire surface of each vehicle, detecting even the most minor defects that human inspectors might overlook. This implementation reduces the rate of surface defects, improves overall quality, and shortens the time required for manual inspections. The automated system provides more consistent and accurate quality control, ensuring all vehicles meet the brand's stringent standards.
Electronics Industry: Component placement and solder joint inspection
Case study: Implementing computer vision in PCB assembly
In a printed circuit board (PCB) assembly plant, the precise placement of electronic components and the quality of solder joints are crucial to electronics manufacturing. Manual inspection was time-consuming and error-prone, resulting in defective products.
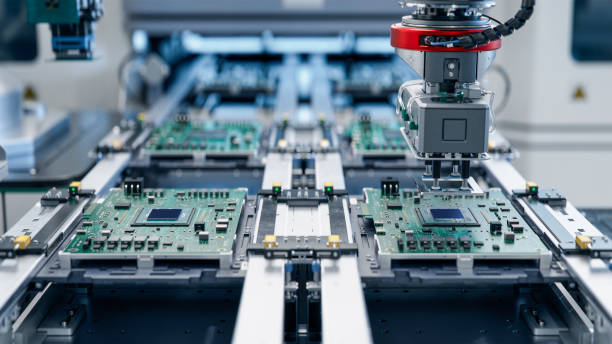
Integrating computer vision systems into their PCB assembly plant allows for automatically inspecting component placements and solder joints. In real-time, the system employs advanced image processing to detect misaligned components, incorrect orientations, and poor-quality solder joints. This enhances the accuracy of component placement and soldering, reducing the number of defective boards produced. It also enables them to scale up production without compromising quality.
Pharmaceutical Industry: Tablet inspection and compliance documentation
Case study: Automated tablet inspection system
Drug manufacturers must ensure that all tablets are free from defects such as cracks, chips, or discoloration while complying with strict regulatory requirements for documentation and traceability. Traditionally, this process relied on written logs or manually captured images, which could be incomplete or inconsistent.
They implemented computer vision software that inspects each tablet on the production line using high-speed cameras. The software captures detailed images of every tablet, automatically identifying and rejecting defective ones while logging inspection data for regulatory compliance. This system enhances defect detection, streamlines documentation, and categorizes defects for comprehensive reporting. During audits, manufacturers can quickly retrieve visual data to demonstrate compliance with industry standards.
These case studies highlight the versatility and impact of computer vision in optimizing production line processes across various industries.
What does it take to develop computer vision software for industry production lines?
Computer vision software is inherently sophisticated, and integrating it directly into the machines or cameras that oversee operations presents more challenges. The complexity increases with the need to manage vast amounts of data for training, maintain model accuracy in real-time environments, and continuously update the system as the production line evolves. Consequently, industries seek scalable solutions for developing, managing, and deploying computer vision software in their production lines.
MLOps platforms serve these purposes effectively. Manufacturing industries typically utilize MLOps platforms from cloud providers such as AWS, Azure, and Google Cloud Platform (GCP) or cloud-agnostic options like Picsellia.
Picsellia is an MLOps platform dedicated to computer vision, designed to help manufacturing industries streamline various aspects of computer vision processes, including image and video management, model training, versioning, deployment, and monitoring. It integrates seamlessly with existing production line requirements and development practices, software, infrastructure, and operations. Key benefits of Picsellia for maintaining scalable computer vision solutions and ensuring smooth integration include:
Efficient data management
Picsellia's data lake connects all your existing production line data sources, providing a centralized hub for annotating and organizing the images or videos used to train your production line models. It employs a unified data model that supports metadata and georeferencing, allowing you to manage images or videos by context. This setup enables easy searching and sorting of data for annotations or training using Picsellia's SQL-like custom data query language.
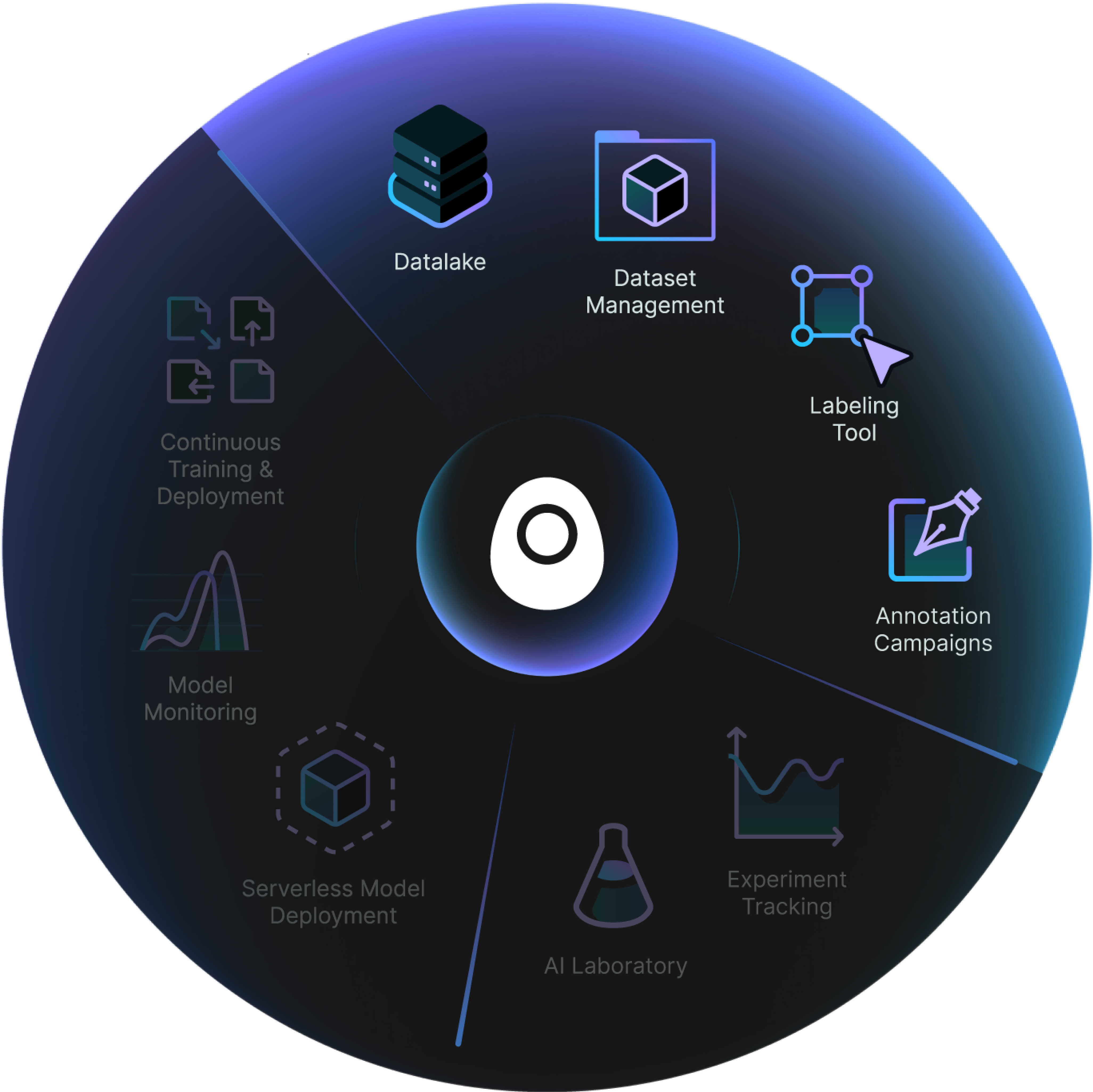
Streamlined development and deployment
Picsellia's AI Laboratory streamlines the development process, enabling industries to prototype, test, and deploy computer vision models quickly. Additionally, Picsellia supports serverless deployments, allowing industries to concentrate on developing solutions rather than managing the underlying computer vision software infrastructure.
Continuous monitoring and maintenance
Picsellia’s automated pipelines provide continuous monitoring of deployed models, including automated alerts and diagnostics, to detect potential issues before they affect production. The platform also supports automated model retraining, utilizing new data from the production line to ensure models remain accurate and current.
Manufacturing industries can overcome the significant challenges of developing, managing, and implementing computer vision software on production lines by using a dedicated MLOps platform like Picsellia. Its technologies enable manufacturers to efficiently scale their solutions, maintain high performance, and continuously improve operations. This leads to greater agility, reduced costs, and increased productivity. Begin building computer vision solutions for your production line with Picsellia today.