Introduction
The integration of computer vision technology in modern manufacturing has opened up a world of possibilities for companies looking to streamline their operations. With the ability to automate visual inspections and more, computer vision is revolutionizing the way manufacturers operate. As we continue to embrace Industry 4.0, the importance of computer vision in manufacturing cannot be understated. In this article, we will explore some trends in computer vision applications in manufacturing and their potential impact in 2023.
Let's delve deeper into the world of computer vision and its impact on manufacturing.
Quality Control & Defect detection
Quality control & defect detection in manufacturing
Quality control and defect detection are crucial aspects of the manufacturing process. Quality control refers to the process of ensuring that a product or service meets the required quality standards. This process involves checking and verifying that all aspects of the product or service, from design to manufacturing, meet the required specifications. Defect detection, on the other hand, involves identifying and eliminating defects in the manufacturing process. Defects can be caused by errors in the production process, equipment malfunction, or subpar materials. In the manufacturing industry, quality control and defect detection are essential to ensure that products meet customer expectations, comply with regulatory standards, and reduce the likelihood of costly recalls or warranty claims.
Challenges faced in quality control
There are still significant challenges that manufacturers face when implementing in quality control processes. Traditional quality control methods, such as human inspection, are time-consuming and can lead to errors due to fatigue or lack of attention. Complexity of products, with more intricate designs and features make it difficult to detect defects. Finally, the need for high precision and accuracy in quality control, especially in industries such as semiconductor, aerospace and medical devices, requires an extremely high level of confidence of verifications.
Top applications of computer vision in quality control
By using cameras and computer vision pipelines, manufacturers can monitor the production process in real-time. Computer vision models can be trained to for several applications in quality control and defect detection in manufacturing. Here are the main ones already in use:
- Visual inspection: Recognize and classify defects in products by analyzing visual data. This can help detect and reject faulty products before they reach customers.
- Dimensional analysis: Measure the dimensions of products and compare them to the desired specifications. This can help ensure that products are manufactured with the correct size and shape.
- Surface defect detection: Analyze the surface of a product to identify defects such as scratches, cracks, and dents. This can help manufacturers maintain high product quality standards.
- Packaging inspection: Inspect packaging materials for defects such as dents, tears, or punctures. This can help ensure that products are delivered to customers in good condition.
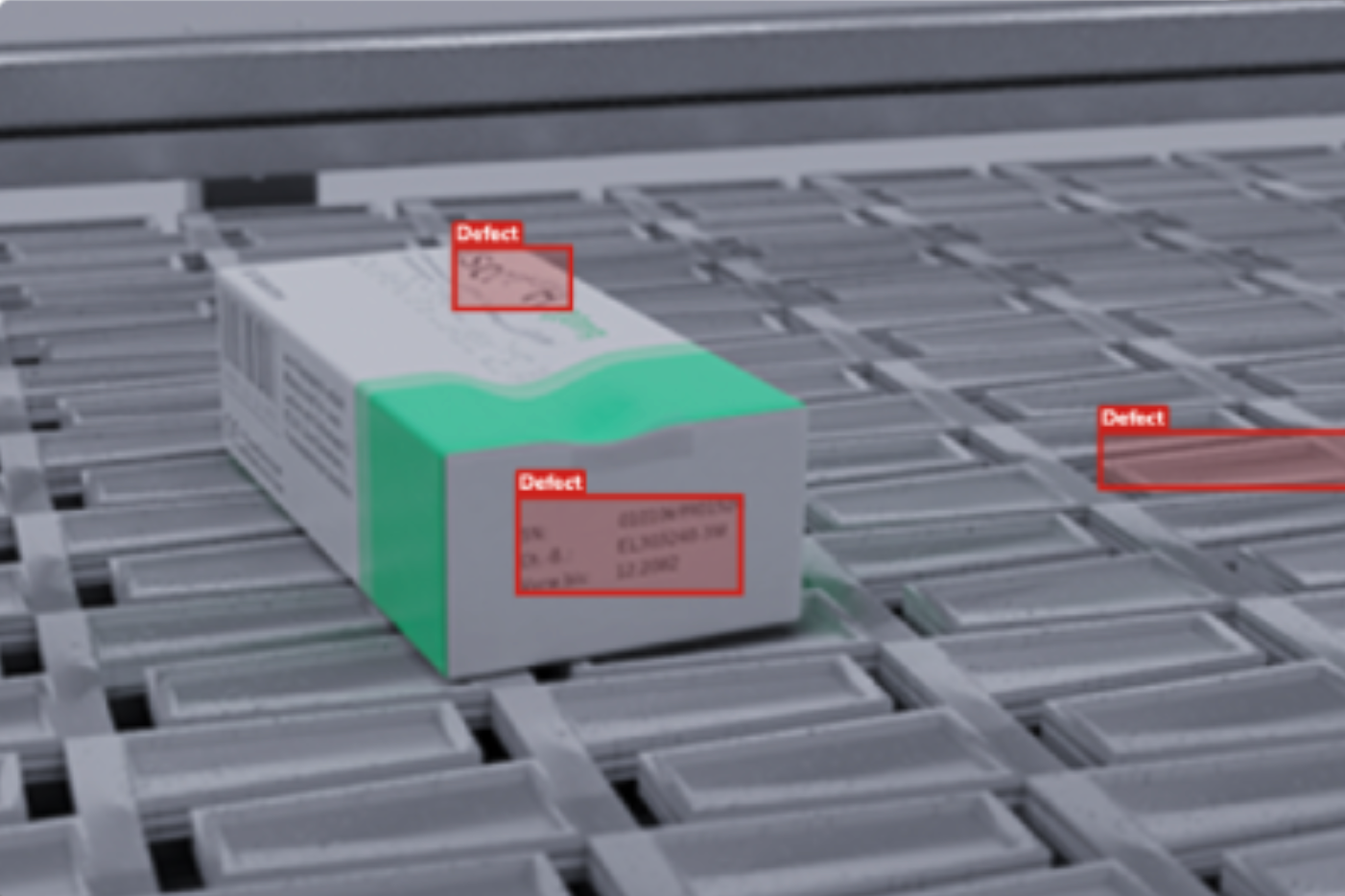
Inventory Management
Explanation of inventory management in manufacturing
Inventory management in manufacturing refers to the process of monitoring, controlling, and optimizing the flow of materials, goods, and products in and out of a manufacturing facility. It involves keeping track of inventory levels, managing supply and demand, and ensuring that there is always enough inventory to meet production needs without overstocking. Inventory management is crucial in manufacturing as it affects the overall efficiency of the production process, and it can impact customer satisfaction and the bottom line of the business. Effective inventory management requires accurate and real-time data on inventory levels and movement, which can be challenging to obtain and analyze manually, particularly in large-scale manufacturing operations.
Challenges faced in inventory management
One of the major challenges in inventory management is inaccurate inventory tracking and stock counts. This can result in stock-outs or overstocks, leading to increased carrying costs, delays in production, and lost sales. Another challenge is the difficulty of identifying and tracking inventory that is stored in multiple locations or moving through different stages of the supply chain. This can lead to inefficiencies, delays, and a lack of visibility into inventory levels and availability.
Top applications of computer vision in inventory management
In the realm of inventory management, computer vision is a game-changer. With its ability to automate processes such as stock monitoring and product recognition, computer vision can help companies optimize their inventory levels, reduce waste, and improve overall efficiency. Some of the top applications in inventory management:
- Stock monitoring: Computer vision-enabled robots can monitor shelves and generate reports with actionable metrics and insights. This application helps companies ensure that their products are properly stocked and reduce waste due to overstocking or under stocking. Real-time inventory tracking can help companies identify slow-moving products and quickly adjust inventory levels to meet demand.
- Product recognition: Another critical application of computer vision in inventory management is product recognition. By analyzing images or videos of products, computer vision can help companies accurately identify and classify products, ensuring that they are properly labeled and stocked in the correct location. This is particularly useful for companies with large and diverse product catalogs. Computer vision technology can also help identify counterfeit products, reducing the risk of selling substandard or unsafe products.
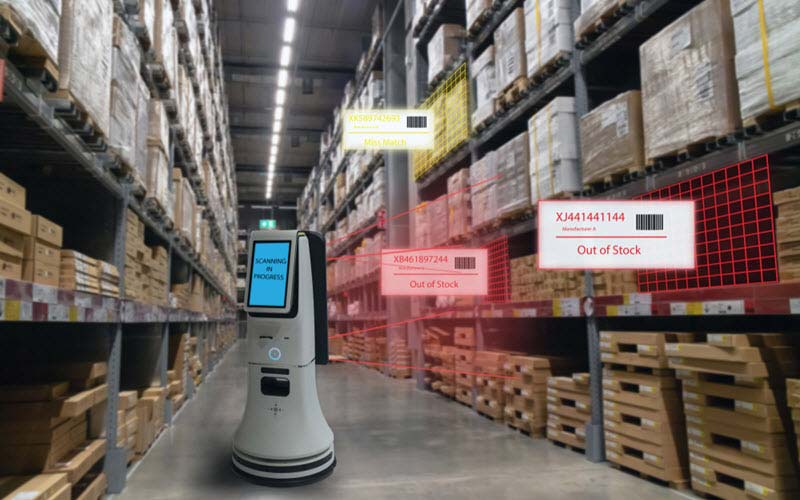
Workers' Safety
Explanation of workers' safety in manufacturing
Worker safety in manufacturing refers to the measures taken to ensure the well-being of workers in a manufacturing environment. It involves identifying and assessing potential hazards, implementing safety protocols and procedures, providing adequate training and personal protective equipment (PPE), and monitoring workers and equipment to prevent accidents and injuries. The goal of worker safety in manufacturing is to create a safe working environment that protects the health and well-being of employees while maximizing productivity and efficiency.
Challenges faced in workers' safety
According to the National Safety Council, the manufacturing industry has one of the highest rates of workplace injuries and fatalities in the United States. In 2019, the manufacturing sector had 417 workplace fatalities, and more than 500,000 non-fatal injuries requiring days away from work.
A major challenge lies in accurately identifying and addressing unsafe behaviors among workers. This includes actions such as incorrect posture, improper equipment handling, or engaging in activities that may lead to accidents and injuries.
Ensuring consistent use of personal protective equipment (PPE) is also crucial to mitigate risks. However, monitoring and enforcing compliance with safety gear, such as helmets, goggles, or safety gloves, can be a complex and ongoing challenge.
Likewise managing fatigue and decrease can significantly impact workers' ability to perform tasks safely. Finally, manufacturing facilities often involve hazardous conditions, such as high temperatures, exposure to chemicals, or heavy machinery. Continuously monitoring these environments and ensuring worker safety in real-time can be a demanding task
Top applications of computer vision in workers' safety
Detect unsafe behaviors and potential hazards before they result in accidents. Here are some key points to consider:
- Detect unsafe behaviors and potential hazards before accidents occur:
- Worker movement analysis: analyze worker movements and identify unsafe actions, alerting workers to correct their posture or stop unsafe behavior.
- Monitoring personal protective equipment (PPE): track whether workers are wearing required PPE, preventing potential injuries and ensuring compliance with safety protocols.
- Thermal monitoring for heat-related safety: monitor employees for signs of heat stress and overheating, particularly in hot and humid environments, enabling early intervention to prevent heat-related illnesses.
- And many others related to predictive maintenance that have a direct impact on workers’ safety.
By leveraging computer vision technology in these areas, manufacturers can significantly improve workers' safety, create safer workplaces, and enhance overall operational efficiency. With real-time monitoring and early detection capabilities, computer vision offers valuable insights and proactive measures to prevent accidents and mitigate potential hazards.
Predictive Maintenance
Explanation of predictive maintenance
Predictive maintenance is a proactive approach to maintenance that uses data analytics, machine learning, and artificial intelligence to predict when equipment or machinery is likely to fail. By analyzing data from sensors and other sources, predictive maintenance systems can identify early warning signs of potential problems and alert maintenance personnel to take corrective action before a breakdown occurs.
Challenges faced in predictive maintenance
Predictive maintenance is crucial in manufacturing because it significantly reduces machine downtime by 30 to 50 percent and extends machine life by 20 to 40 percent, resulting in improved productivity, cost savings, and operational efficiency. [Source: McKinsey]
Predictive maintenance in manufacturing faces several challenges. Determining the optimal time for maintenance activities is a complex task, as it requires accurately identifying the right timing based on equipment condition and performance. Predicting equipment failures is crucial to minimize downtime and costly repairs, but accurately identifying early warning signs and potential failure patterns is challenging due to the vast amount of data generated by modern machinery. Additionally, ensuring equipment safety is a key challenge, involving the detection of wear and tear, identification of safety hazards, and implementation of preventive measures to protect worker safety.
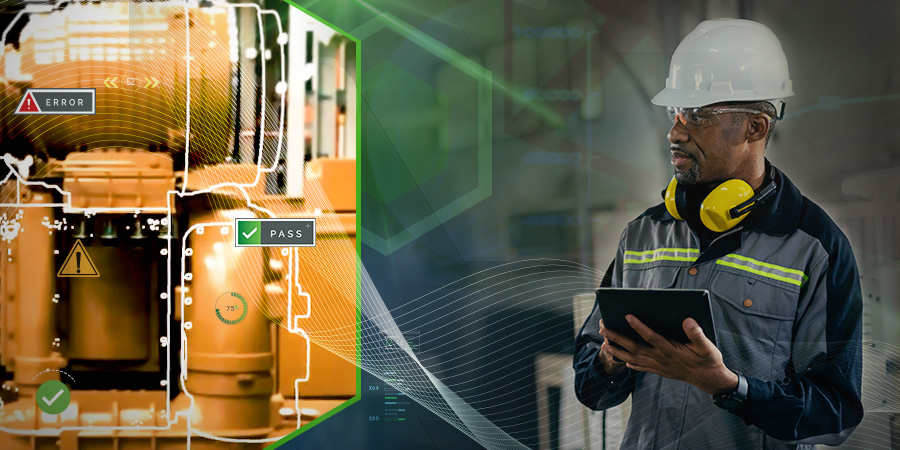
Top applications of computer vision in predictive maintenance
In predictive maintenance, computer vision technology offers valuable applications that transform maintenance practices and deliver significant benefits:
- Optimized Maintenance Planning: Real-time visual data analysis allows maintenance teams to accurately assess equipment condition and performance. This enables precise timing for maintenance tasks, minimizing downtime and optimizing resource utilization.
- Early Equipment Failure Prediction: Automating the analyzes of real-time images and historical records, helps identify patterns and anomalies that signal potential equipment failures. Proactive measures, such as component replacement or repair, can be taken to prevent breakdowns and optimize operational efficiency.
- Equipment Safety Monitoring: Intelligent monitoring systems incorporating visual inspection technologies enable continuous monitoring of equipment conditions. This facilitates the detection of wear and tear, identification of safety hazards, and timely preventive actions, enhancing workplace safety.
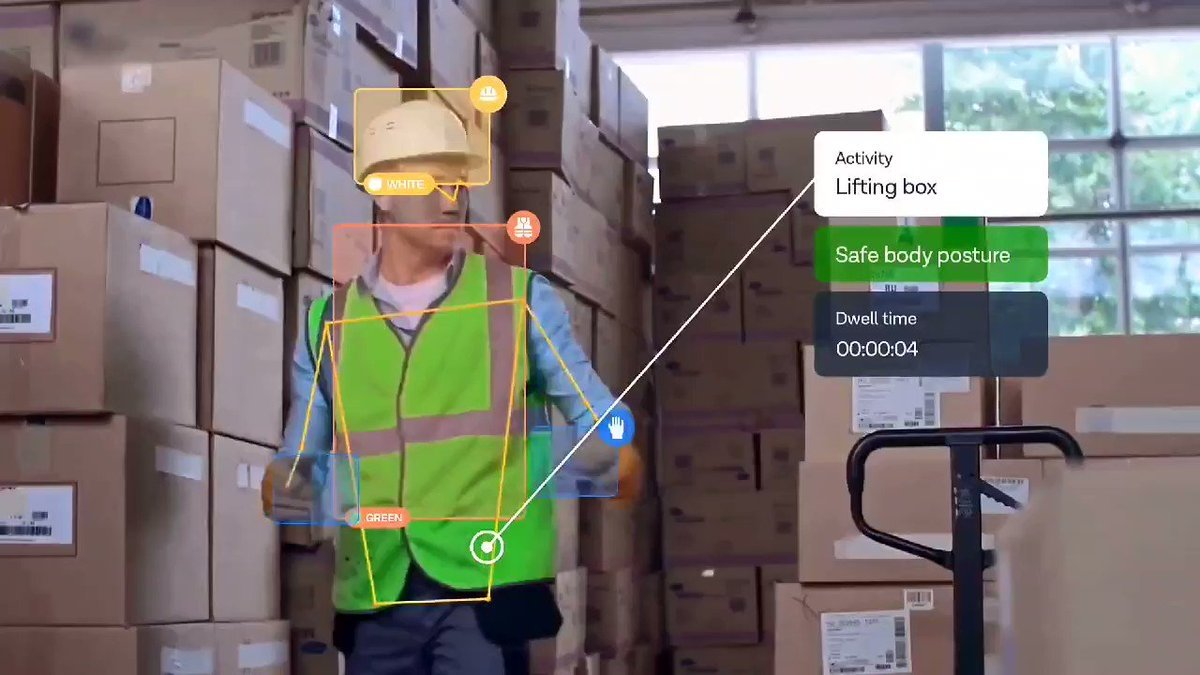
https://www.dailysabah.com/
These computer vision applications empower manufacturers to improve maintenance planning, anticipate equipment failures, and ensure equipment and worker safety. By harnessing the power of computer vision in predictive maintenance, businesses can drive efficiency, reduce costs, and enhance overall operational performance.
Conclusion:
In conclusion, the integration of computer vision in manufacturing has brought about a paradigm shift in the industry. It is revolutionizing the way things are done, and it's safe to say that we are in the era of Industry 4.0.
With its ability to perform complex tasks, improve quality control, optimize supply chains, and enhance worker safety, computer vision is set to revolutionize the manufacturing industry. The numerous applications outlined above are just the beginning of what is possible.
Manufacturers can leverage CVOps tools like Picsellia to implement robust computer vision pipelines, gain real-time insights, streamline operations, and improve overall productivity. As the manufacturing industry continues to evolve, the integration of computer vision will play an increasingly important role in shaping its future.
The best is yet to come – let’s watch this space!